Drilling – A Physical Science
The process of geothermal drilling is a physical science. Operators must be very experienced to adapt to the differences that emerge in ground types, ground loop designs and site space constraints. The weather can impact works and drastically alter on site conditions and safety. No matter what anyone says, no one can know the full ground conditions until a hole is drilled to full depth.
Geothermal drilling equipment can be simple or technically very advanced. The countless differences in geological formations and the physical aspects of each individual site come into play. The selection of equipment for the job will determine the success of a drilling program. Competent and highly experienced personnel will save money and time on a job.
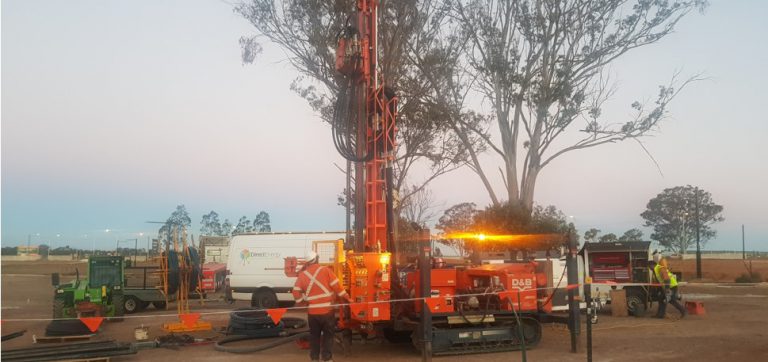
Specialised Drill Rig Fleet
We own and deploy several different types of drill rigs that can be applied to geothermal systems requiring vertical or slanted drilling. Highly specialised radial drill rigs are used for tight space drilling in situations where limited ground area is available for installation. Other drill rigs are used in basements for large building retro-fit projects. These have the lowest head room requirements of all our rigs. Truck-mounted and track-mounted rigs are utilised to establish geothermal aquifer systems and water bores, which can range from shallow to very deep bores. We own and operate drill rigs to undertake any scale of closed loop geothermal and open aquifer geothermal to 300 metres depth.
Ground Radial Drilling and Vertical Drilling can be applied to the same site, with the GRD method allowing in excess of 2000 metres of ground loop in a single square metre of a site. GRD has extremely low site impact and is the most efficient space saving method of geothermal drilling in the world.
Ground Radial Drilling (GRD) – Space Saving Technology
Ground Radial Drilling allows for geothermal bore holes to be placed where most architects and engineers would consider it not possible to install a geothermal heating and cooling system. It creates opportunities to obtain energy efficient heating and cooling in very confined site areas. Limited land area is often one of the key barriers to installing a ground loop array in a grid shaped pattern due to the required separation of the ground loops, from 6 to 10 metres apart. We are the only company in Australia that utilises radial drilling rigs and installs GRD geothermal systems. These rigs can also be used for vertical bore holes. Thus, we are the market leader in reduced land area geothermal drilling. We offer full design and installation services to both residential and commercial projects.
Ground Radial Drilling was developed in Germany, by Tracto Technik, an advanced drilling technology company. Thermal modelling for radial ground loops, shown below, offer superior performance via enhanced loop separation, reducing the metres of drilling required to support geothermal heating & cooling systems.
The advantages of radial drilling are unparalleled.
- There is no waste that can be discharged onto the natural ground. All waste is contained within the drilling chamber and pumped into a waste disposal unit.
- The manifold, contained wholly within the drill chamber, reduces the space required in the plant room and thus reduces the mechanical plumbing scope within the building. This significantly reduces the cost of plant room installation.
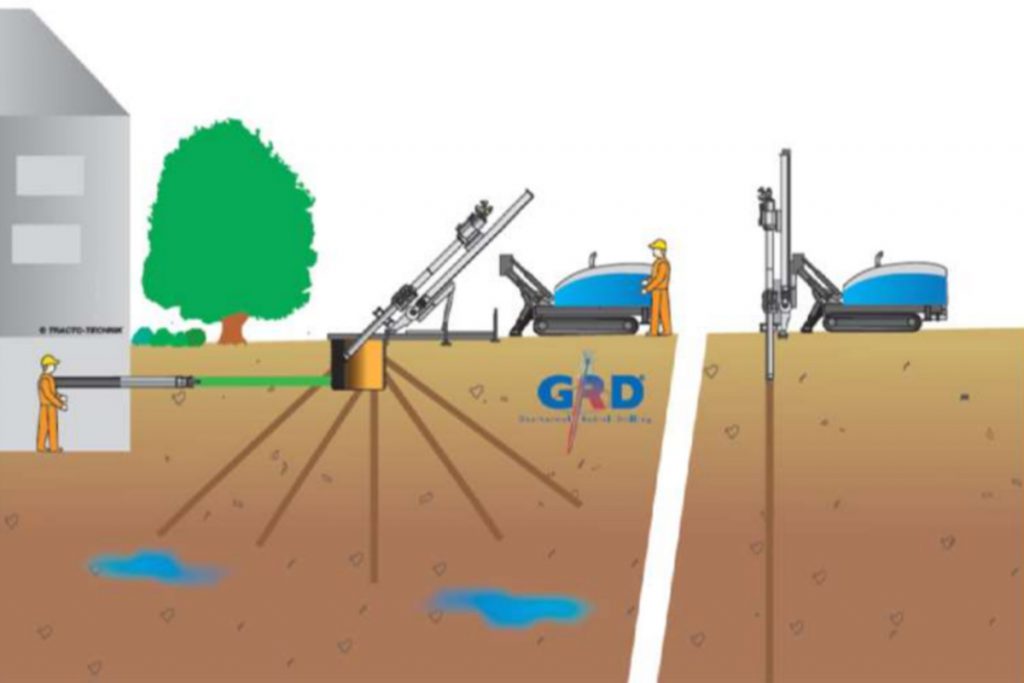
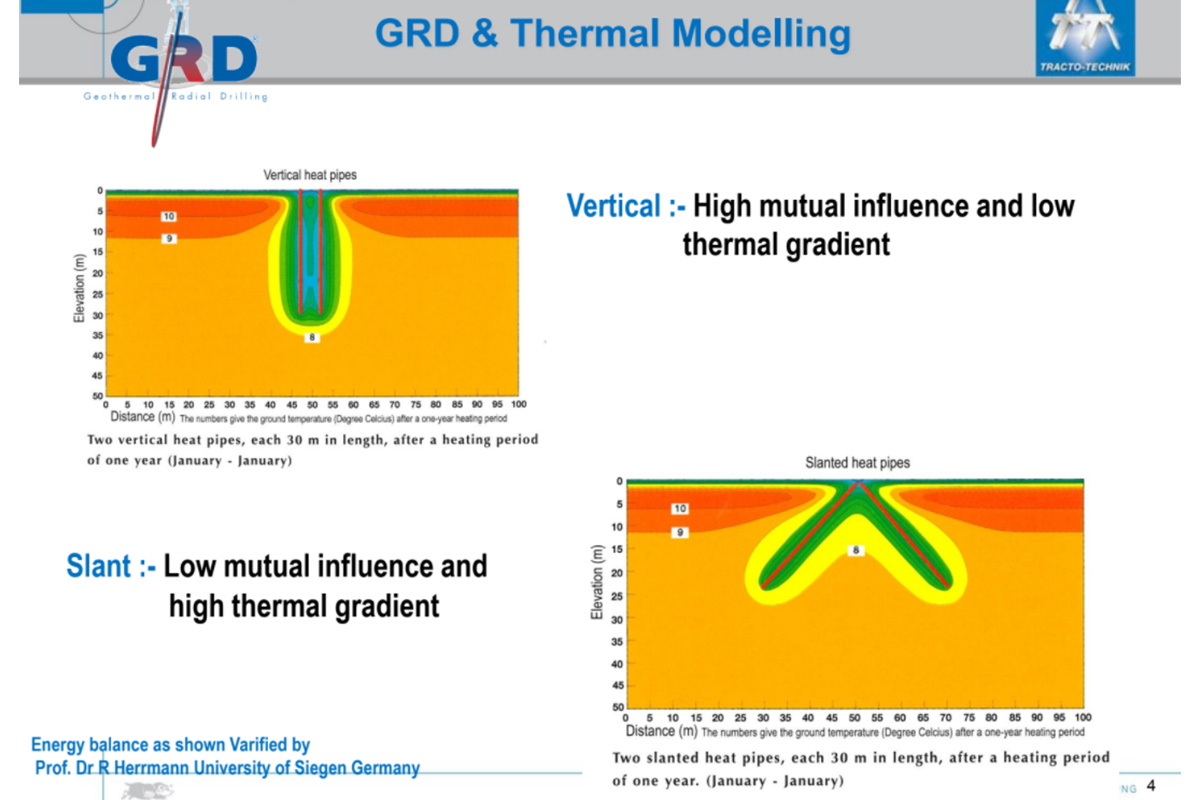
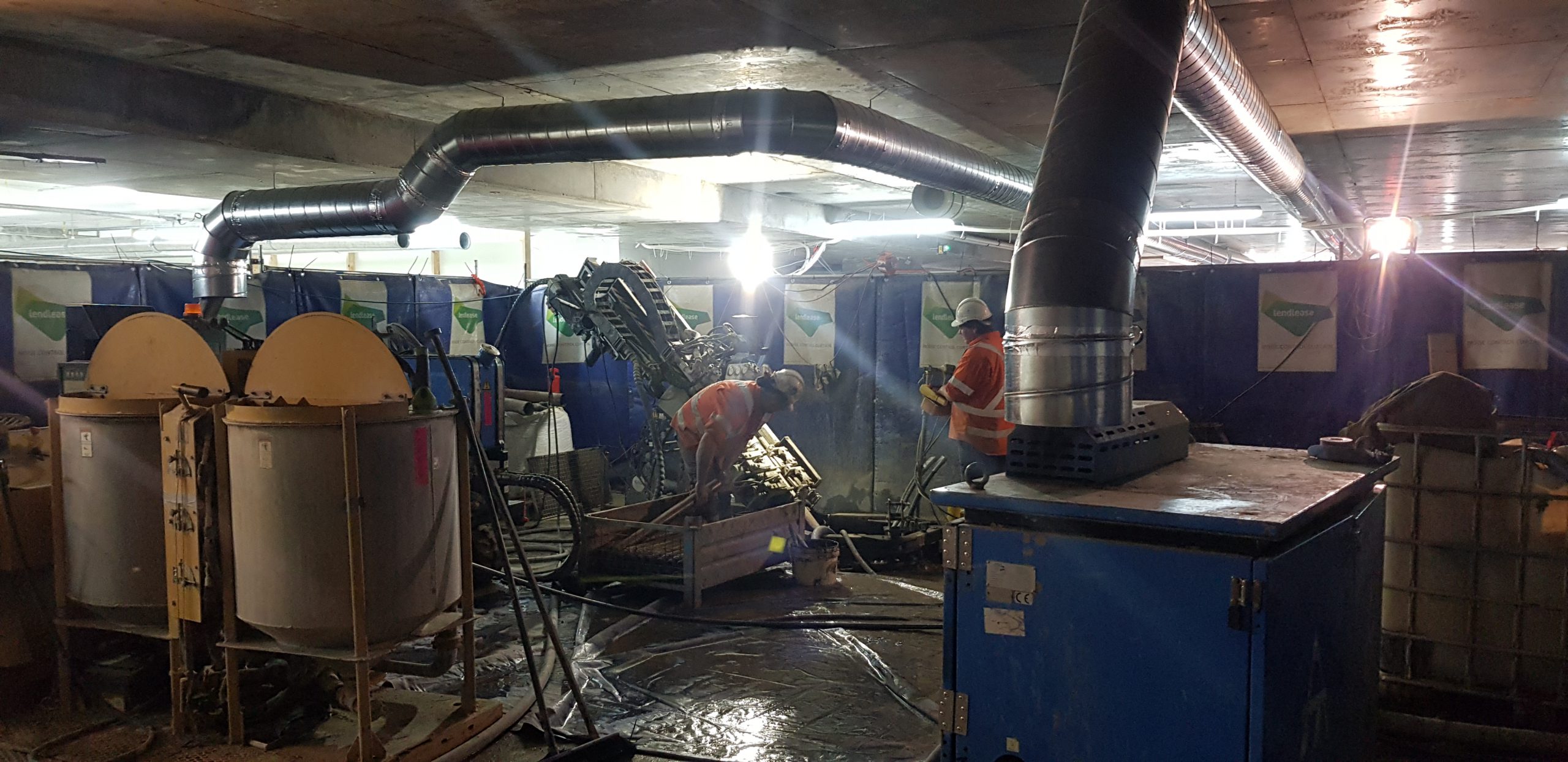
GRD: History of Success
Our history of GRD systems design and installation extends over 8 years, from 2015. The use of GRD ground loop arrays has been applied to critical infrastructure, aquatic, commercial & residential projects in NSW, Victoria, South Australia and Western Australia.
Our ability to install large scale geothermal systems in the critical path timeframes demanded by most major projects is proven over many years of operation. With our fleet of advanced radial & vertical drill rigs, we can deploy multiple rigs on a single site if required, significantly reducing the time frame of installations without an impact on the project timeline. We can meet the strictest project deadlines as required.
Our clients include some of Australia’s most prominent Project Proponents, including global companies Acciona, Lend Lease and the Fraser’s Property Group.
Geothermal Drilling Logistics: Project Management
On site, Project Managers must juggle trades and ensure that different trades can work effectively together on very limited site areas. Our radial drilling allows this to happen much more easily than the area-hungry vertical bore hole arrays. The benefit of this is appreciated by builders who need to undertake geothermal drilling simultaneously with other onsite construction activities.
The drilling process is undertaken in parallel to building construction, with both site plumbing/electrical pre-lay occurring adjacent to the drill chamber location. The adjacent photo shows the drilling area at a mere 1m2 area in a garden bed location. Radial drilling provides no impost on site obstructions or service conflicts with a dual pipe system only to the plant room. All drilling activities can be undertaken prior, during or after the construction of the building and sit within or outside the building footprint.
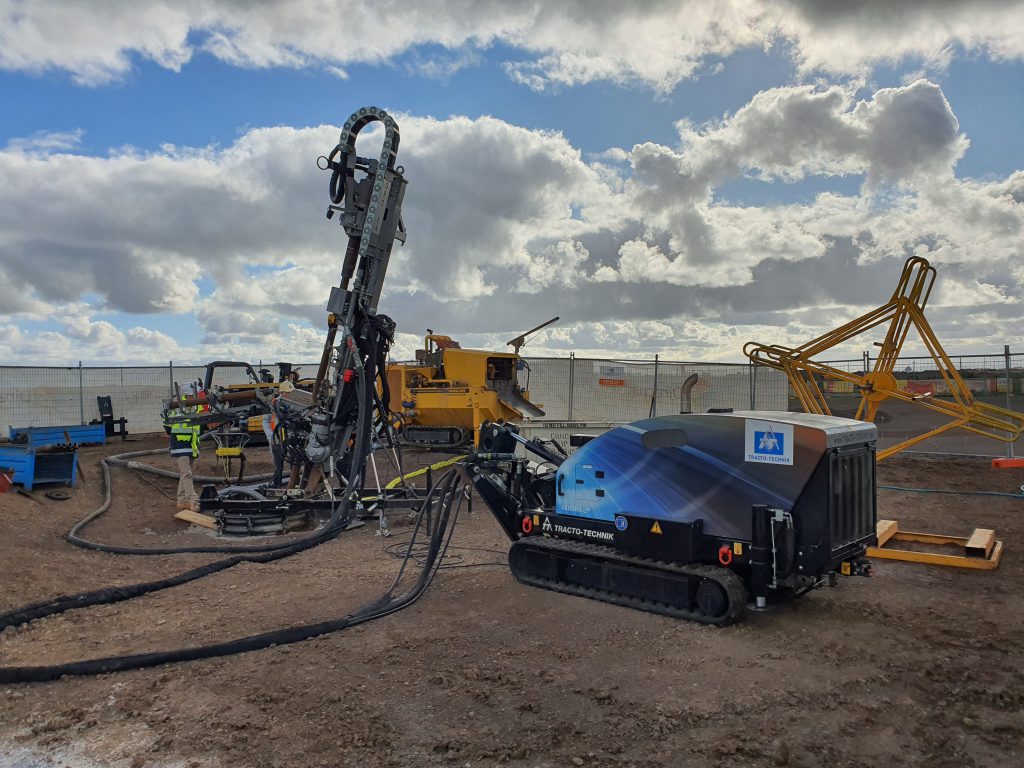
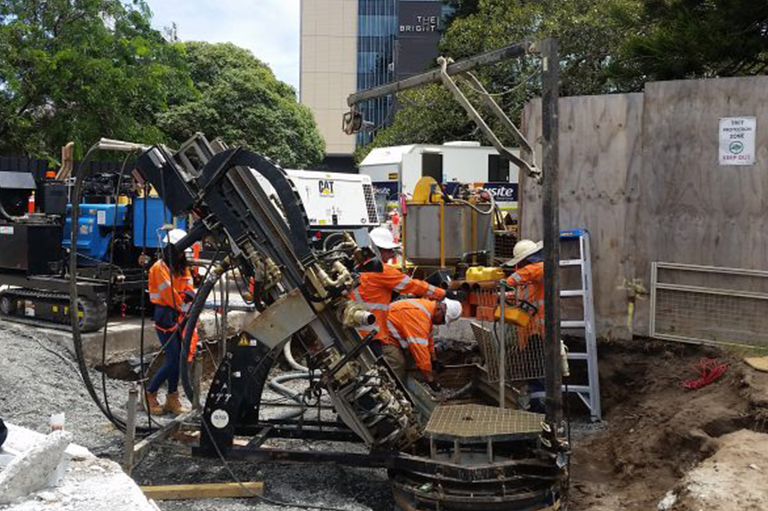
Occupational Health & Safety
On site health and safety of drilling personnel and those within the vicinity of the drilling operation is the most important aspect of the drilling process. We focus on attaining best practice standards and align with all necessary State and Federal safety obligations.
Maintaining the excellent safety standards of Australia’s leading developers and construction companies is our OH&S modus operandi. We deploy equipment that keeps the sites as clean as possible, enhancing the safety standards for all those involved in the ground loop array installation process.
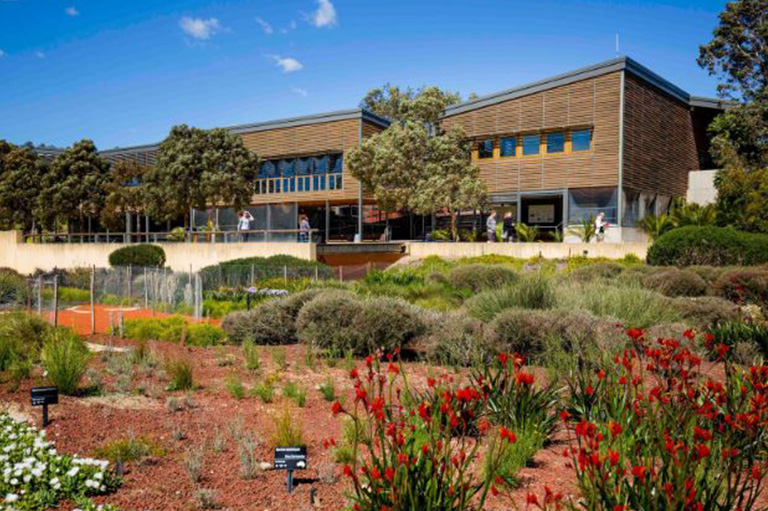
The Natural Environment
The drilling process involves the extraction of material from underground. We aim to protect the natural environment via the use of the latest waste disposal and containment measures. We minimise water use and recycle water in our drilling process to meet best practice standards. Our environmentally sensitive drilling techniques minimise both the impact to the worksite and the environment. Where possible we use a closed system of drill cuttings extraction and water circulation.
In sites that require off site waste removal all drill cuttings are contained and moved offsite to preferred waste processing facilities.